I principi della lubrorefrigerazione
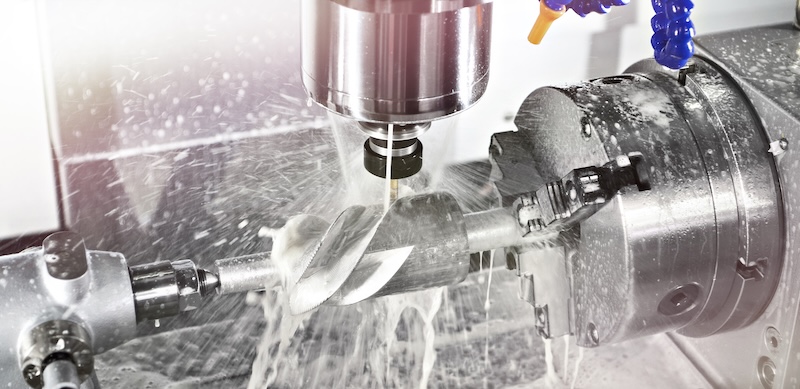
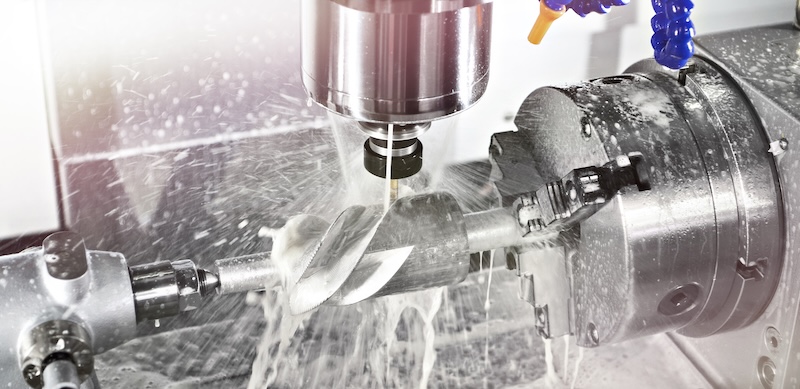
Da semplice fluido a sistema: la complessità della lubrorefrigerazione investe la riuscita di ogni lavorazione meccanica.
Lubrorefrigerazione significa essenzialmente scegliere il fluido da taglio? Questo forse era vero in passato, ma oggi è chiaro come la questione sia ben più complessa: non è più solo lubrificare e raffreddare, ma è richiesto anche un impatto decisivo sulla lavorazione. E questo in termini di qualità e di performance, quindi, in ultima analisi, di costi. E quindi di marginalità e competitività.
Studi e ricerche hanno portato, negli anni, a una nuova consapevolezza e a un’evoluzione del sapere, tanto che si sta facendo velocemente strada la concezione di sistema di lubrorefrigerazione, che copre tutto il processo: dalla scelta del fluido, alla sua manutenzione, per arrivare allo smaltimento degli esausti e alla sostenibilità, senza tralasciare la salubrità dell’ambiente di lavoro e la salute degli addetti.
Dunque parlare di lubrorefrigerazione significa affrontare un mondo estremamente variegato e complesso, che gioca un ruolo centrale nel processo produttivo. Questa centralità, con tutti i risvolti che ne conseguono, sta spingendo studi e ricerche che coinvolgono sia i produttori di lubrorefrigeranti che le aziende manifatturiere e i poli di ricerca.
Questi approfondimenti stanno portando a una continua evoluzione del concetto stesso di lubrorefrigerazione, e all’individuazione di nuove soluzioni, o strategie, spesso altamente innovative. Una lubrorefrigerazione 2.0?
La premessa
Dato che la tribologia è la scienza e la tecnologia delle superfici interagenti, con la presenza di lubrorefrigerante durante una lavorazione si va proprio a modificare come interagiscono le superfici a contatto e in moto relativo. Senza soffermarsi sui vari tipi di lubrorefrigeranti, e relativi additivi, vale la pena considerare quali sono i compiti da assolvere e perché.
Durante le lavorazioni meccaniche i fluidi da taglio hanno la funzione primaria di raffreddare e lubrificare, riducendo in questo modo l’attrito e la conseguente generazione di calore, consentendo, fra l’altro, di avere migliori qualità superficiali. Se l’effetto refrigerante aumenta la durata dell’utensile, mantenendo la temperatura al di sotto della temperatura detta di “softening” termico del materiale, riducendo l’usura di natura termica, l’effetto lubrificante riduce l’usura meccanica del tagliente. Ai lubrorefrigeranti sono richieste anche diverse funzioni secondarie, come il trasporto di trucioli e la pulizia degli utensili e del pezzo lavorato.
La natura stessa dei fluidi da taglio porta con sé problemi legati all’ambiente e alla salubrità, che vanno adeguatamente considerati. Ne sono un esempio l’inquinamento dovuto alla dissociazione chimica alle alte temperature di taglio, l’inquinamento delle acque, la contaminazione del suolo durante lo smaltimento degli esausti, nonché problemi biologici e di natura sanitaria per gli addetti.
Dalla lubrificazione alla deriva termica
La funzione lubrificante è il primo obiettivo della lubrorefrigerazione, ovvero la riduzione degli attriti nella zona di taglio. Detto ciò, è evidente come una buona capacità lubrificante del prodotto in uso sia fondamentale, con un forte legame emulsivo con l’acqua di miscela e una buona stabilità, anche in caso di alte percentuali di olio (15÷18%) e lavorazioni con pressioni elevate (30÷100 bar, e oltre), evitando che la molecola si spezzi, che ci siano accumuli di oli estranei in vasca e la presenza di schiume. La presenza di schiume deve subito attivare un alert perché, oltre al rischio di tracimazione, cambia lo stato del lubrorefrigerante che, da stato fluido allo stato liquido, diventa un mix di liquido e gas, quindi con caratteristiche chimico-fisiche molto diverse rispetto allo stato iniziale.
La funzione lubrificante viene espletata pienamente solo se l’emulsione è pulita, cioè pressoché priva di sostanze inquinanti e particelle metalliche, che si comporterebbero come un additivo abrasivo nella zona di taglio, e di parti oleose di natura diversa. La presenza di parti oleose, sottoposte allo stress dovuto alle forze di taglio, tendono a scindersi, provocando fumi o nebbie, che, oltre ad essere dannose per l’ambiente, possono liberare vapori potenzialmente aggressivi nei confronti sia della superficie del pezzo in lavorazione che della macchina utensile.
La sfida della lubrorefrigerazione
Raffreddare significa asportare il calore che si genera durante l’azione di taglio da parte dell’utensile. Il volume di lubrorefrigerante in circolazione continua è una quantità ben definita, ed è questa quantità che assorbe tutto il lavoro, dovuto alla sua compressione nelle pompe di rilancio, e tutto il calore legato all’operazione di taglio: è una situazione molto comune non riuscire a disperdere naturalmente il calore accumulato, che porta ad un innalzamento della temperatura del fluido circolante (40÷50°C, e oltre).
Si tratta di una condizione sfavorevole perché comporta una forte evaporazione e, di conseguenza, una variazione anche elevata della concentrazione, un aumento dell’instabilità del legame emulsivo, dovuta alla variazione di concentrazione, e un aumento della proliferazione batterica nelle vasche, che è accelerata proprio dall’innalzamento di temperatura. Le conseguenze possono essere disastrose, sia per quanto riguarda la stabilità del fluido, che per la possibilità di formazioni di mucillagini, funghi… oltre alla formazione di cattivi odori.
Il controllo della deriva termica, che va oltre il semplice raffreddare, favorisce la stabilità termica del binomio macchina utensile–pezzo in lavorazione, con una ricaduta importante sull’efficienza del processo produttivo: è noto infatti come l’alterazione di questo binomio porti inesorabilmente alla produzione di scarti.
Inquinanti: chi sono
La varietà e la differenziazione degli inquinanti, che non sono solubili nel fluido da taglio, è notevole, ma può essere schematizzata secondo tre macrofamiglie:
- Prodotti lubrificanti e protettivi (vernici comprese) che vengono utilizzati per produrre o proteggere sia la macchina utensile che i pezzi da lavorare.
- Particelle abrasive e particelle metalliche. Le prime sono depositate sui pezzi come residuo delle lavorazioni precedenti, mentre le seconde si generano durante il processo produttivo. La dimensione degli inquinanti di questa macrofamiglia è mediamente di 8÷20 µm, anche se, in alcuni casi, si possono avere dimensioni massime di qualche micron se non addirittura meno.
- Colonie di batteri che si formano all’interno del lubrorefrigerante, trovando un habitat favorevole alla loro proliferazione proprio in fluidi sporchi e poco ossigenati.
Data questa realtà inconfutabile, dovrebbe essere inevitabile chiedersi: «Cosa va fatto per mantenere il fluido il più possibile nelle condizioni iniziali?»
Monitoraggio e manutenzione
Come per qualsiasi componente del sistema macchina utensile, anche il fluido da taglio deve essere oggetto di monitoraggio. Infatti, un lubrorefrigerante lavorerà bene e a lungo solo se sarà usato in modo adeguato e se verrà eseguita una regolare manutenzione che preveda un controllo delle caratteristiche e della composizione, che devono essere conformi alla scheda tecnica del prodotto.
Lo stato del lubrorefrigerante deve quindi essere monitorato di continuo in modo da rilevare tempestivamente situazioni inadeguate che, altrettanto tempestivamente, vanno corrette. Controllo e manutenzione preventiva sono determinanti ai fini della durata del fluido e della sua efficacia, a garanzia di una lavorazione performante e di qualità.
Ad umido o a secco?
Una delle grandi sfide tecnologiche della fine del secolo scorso riguardava la possibilità di eliminare l’uso dei lubrorefrigeranti, per rispondere alle nascenti esigenze in tema ambientale, oltre che economico. In quest’ottica sono nate le tecniche NDM (Near Dry Machining) che prevedono l’eliminazione completa o parziale del fluido da taglio, ritenute il miglior approccio per raggiungere il più alto livello di ecosostenibilità della lavorazione, abbattendo, al contempo, i costi di processo.
Viene utilizzato un aerosol, ovvero una nebbia fine composta da una miscela aria-olio, spruzzato in direzione del tagliente ad una pressione adeguata al tipo di lavorazione, con una portata dell’ordine di 1–100 cm³/h, che rappresenta circa un decimillesimo della portata in caso di lavorazione tradizionale. La lubrorefrigerazione MQL (Minimum Quantity Lubrication), ne è un esempio noto.
La lavorazione a secco, che non prevede utilizzo alcuno di olio o emulsione, può essere vista come una ulteriore evoluzione dell’MQL, resa possibile dalla continua evoluzione tecnologica tanto delle pratiche progettuali che dei materiali per utensili. In questo caso viene sfruttata aria in pressione, veicolata attraverso fori in genere praticati sullo stelo dell’utensile, che, pur non avendo alcuna funzione lubrificante e con un blando effetto sulla riduzione del calore, ha però un grande potere di evacuazione del truciolo.
E allora: lavorazione a secco? Sì e no. Difficile dare risposte assolute. La lavorazione a secco sarebbe auspicabile, ma non può essere impiegata su tutti i materiali e, naturalmente, richiede utensili specificatamente studiati, con superfici in grado di ridurre la frizione e l’incollamento del truciolo. Oltre che metallo duro o rivestimenti appositamente studiati. In alcune applicazioni la lavorazione a secco può essere una soluzione estremamente interessante ma, nella maggior parte dei casi, refrigerazione e lubrificazione restano indispensabili.
Il decadimento del lubrorefrigerante
L’impiego del lubrorefrigerante ne determina il decadimento che dipende da una concomitanza di fattori con, in primis, l’inevitabile presenza di contaminazioni, quali perdite di olio dei sistemi di lubrificazione o da quelli idraulici, impurità, di varia dimensione, rilasciate dal pezzo in lavorazione e inquinanti legati all’ambiente e alla presenza dell’uomo.
Quali sono le caratteristiche da tenere sotto controllo per rilevare lo stato di salute del fluido? Sono diverse e dipendono fortemente dal tipo di fluido e dalla lavorazione ma, in linea generale, i principali parametri da monitorare sono:
- la concentrazione
- il valore del pH e della alcalinità
- il controllo della protezione anticorrosiva
- il controllo della stabilità
- la determinazione dell’eventuale contaminazione batterica
L'articolo I principi della lubrorefrigerazione sembra essere il primo su Meccanica News.
Qual è la tua reazione?






