Manifattura Additiva, perché è importante validare i processi produttivi e certificare il prodotto
Nonostante i numerosi vantaggi offerti, la manifattura additiva non si è ancora affermata come tecnica di riferimento in alcuni settori che pure potrebbero trarne grande beneficio. Tra i principali ostacoli alla sua diffusione vi sono la rapida evoluzione tecnologica, la limitata esperienza sui comportamenti a lungo termine dei prodotti realizzati con questa tecnologia e la complessità del quadro normativo, ancora in via di sviluppo e spesso poco conosciuto. In questo articolo Paolo Gianoglio analizza il ruolo della conformità di processi e prodotti come fattore chiave per superare queste barriere e favorire l’adozione della manifattura additiva. L'articolo Manifattura Additiva, perché è importante validare i processi produttivi e certificare il prodotto proviene da Innovation Post.
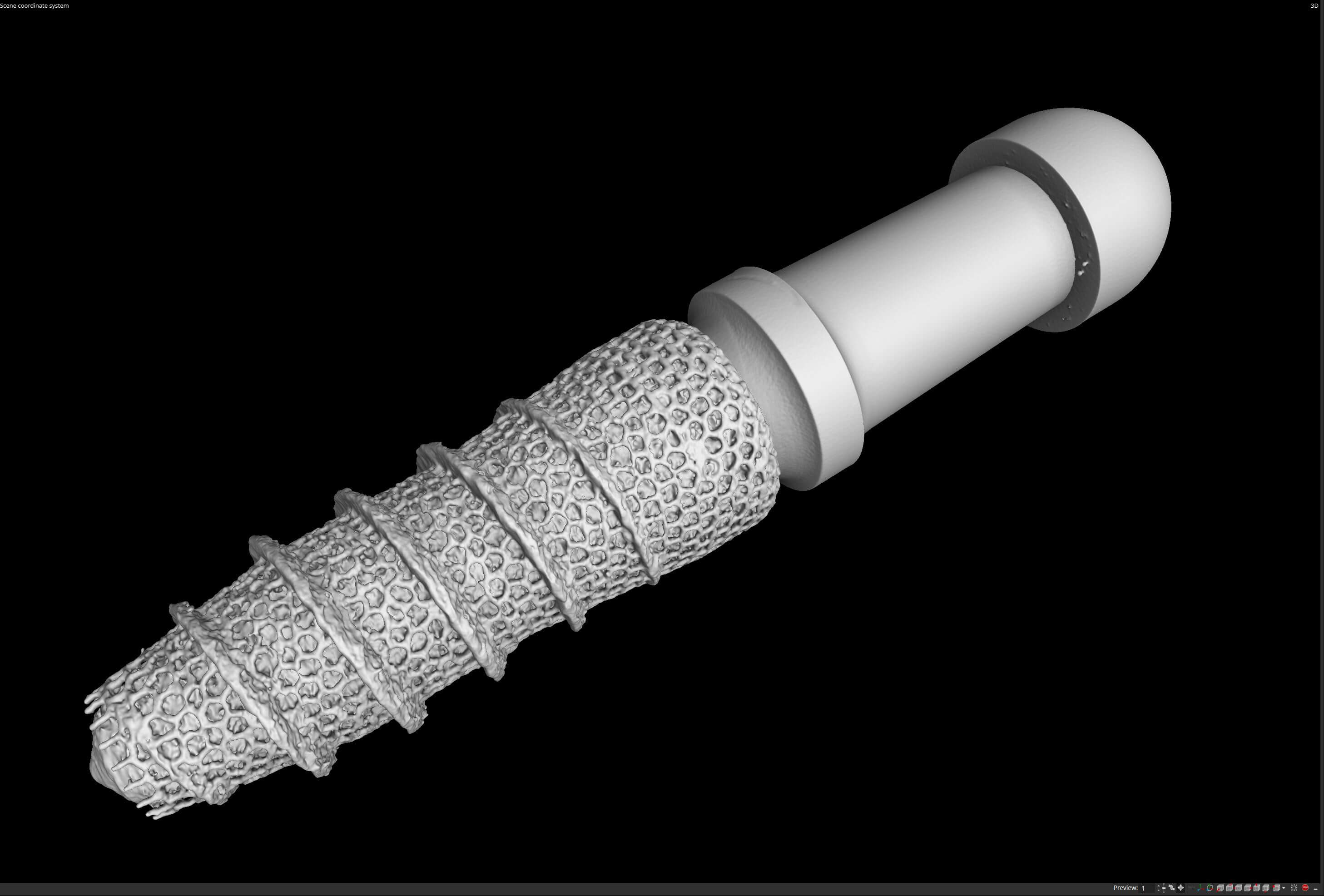
Era la fine del 2016, tutti iniziavamo a prendere confidenza con il termine “Industria 4.0” e con le cosiddette “tecnologie abilitanti”. La ruota delle meraviglie presentata dall’allora Ministro Calenda diventava uno strumento di diffusione di nuovi concetti ma anche uno strumento di marketing. In mezzo c’era un po’ di tutto, tecnologie già affermate che necessitavano di essere adottate da un maggior numero di imprese e nuove tecnologie che ancora dovevano sviluppare le proprie potenzialità. Tra quest’ultime sicuramente la Manifattura Additiva prometteva grandi trasformazioni del modo di produrre, con vantaggi in termini di qualità, prestazioni, sostenibilità.
Le cause di questa (ancora) limitata adozione sono molto articolate e complesse, e questo articolo non ha sicuramente l’obiettivo di indagarle compiutamente. Vogliamo invece concentrare l’attenzione sul tema della conformità dei processi e dei prodotti e come questo aspetto potrebbe contribuire almeno in parte a superare alcune delle barriere all’adozione.
Gli ostacoli ad un’adozione più ampia della Manifattura Additiva
Quando ci riferiamo alla Manifattura Additiva stiamo in effetti parlando di un concetto relativamente nuovo, che al proprio interno raggruppa tecnologie diverse, applicate a diversi materiali. È un contesto caratterizzato da una rapida dinamica di innovazione e da una forte propensione alla sperimentazione di nuove soluzioni. Abbiamo ancora un’esperienza limitata sul comportamento dei prodotti realizzati in Additive nel corso della loro vita utile, molte applicazioni sono state realizzati solo negli ultimi anni.
Ogni tecnologia presenta aspetti peculiari, vantaggi e criticità che la rendono più o meno indicata per determinati utilizzi.
I principali settori di applicazione – Aerospace, Energy, Medicale, Automotive – sono caratterizzati da particolari esigenze di prestazioni e sicurezza, da un contesto normativo consolidato, da prassi di settore molto restrittive e spesso da requisiti cogenti per l’immissione sul mercato.
Il contesto normativo specifico, benché già ricco, è in costante evoluzione, molto complesso, purtroppo ancora poco conosciuto e diffuso. In Italia i lavori normativi in ambito Additive sono seguiti dal CT 529 (Uninfo) che partecipa a partecipa alle attività dei CEN/TC 438 e dell’ISO/TC 261. Nell’ultimo Businnes Plan pubblicato (rev. 4 del 22/9/2022) il Comitato ISO/TC 261 “Additive manufacturing” ha confermato la struttura della normazione in ambito Additive.
Al contrario, quando la sperimentazione di nuove soluzioni avviene in azienda, con acquisizione di competenza attraverso metodologia “trial & error” spesso si affrontano problemi per i quali esistono già soluzioni definite (a partire dal Design for additive manufacturing).
Si percepisce quindi un’importante esigenza di coinvolgimento da parte di tutti gli attori (Università e centri di ricerca, imprese, enti normatori, associazioni) per mettere a fattor comune la conoscenza e includere tra i temi cruciali la qualifica e la certificazione di materiali, processi, competenze e prodotti.
Normazione, certificazione e testing
Standard e normative sono fondamentali per garantire consistenza, sicurezza e qualità dei prodotti. Le norme sono strumenti condivisi che consentono a produttore e cliente di incontrarsi su un terreno comune e non arbitrario che definisce i requisiti di un materiale, un processo, un componente o un prodotto. Tuttavia, il contesto che riguarda la manifattura additiva è in costante evoluzione e non copre ancora tutte le necessità con la medesima granularità. I principali motivi delle lacune, già evidenziati, sono:
- La manifattura additiva è un processo relativamente giovane con elevati tassi di innovazione;
- Gli aspetti da tenere in considerazione quando si utilizza questa tecnologia sono molteplici, poiché numerosi sono i fattori che possono influenzare qualità e caratteristiche del prodotto finale, dalla scelta e validazione della tecnologia, alla produzione vera e propria.
Occorre inoltre considerare che ogni settore e ogni mercato prevedono disposizioni legislative e normative specifiche che riguardano le caratteristiche di materiali e prodotti e che prescindono dal processo produttivo. Se per esempio produco un dispositivo medico destinato al mercato europeo, dovrò preoccuparmi di soddisfare i requisiti del Regolamento Europeo UE n. 2017/745 (MDR) che definisce specifici requisiti di carattere generale quali ad esempio il seguente:
I dispositivi sono progettati e fabbricati in modo tale da garantire che siano soddisfatti i requisiti relativi alle caratteristiche e alle prestazioni di cui al capo I. Una particolare attenzione va rivolta agli elementi seguenti:
-
- a) scelta dei materiali e delle sostanze utilizzati, in particolare dal punto di vista della tossicità e, se pertinente, dell’infiammabilità;
- b) compatibilità tra i materiali e le sostanze utilizzati e i tessuti biologici, le cellule e i fluidi corporei, tenendo conto della destinazione d’uso del dispositivo e, se del caso, assorbimento, distribuzione, metabolismo ed escrezione;
- c) compatibilità tra le diverse parti di un dispositivo che consiste di più di una parte impiantabile;
- d) impatto dei processi sulle proprietà dei materiali;
- e) se del caso, i risultati della ricerca biofisica o modellistica la cui validità sia stata precedentemente dimostrata;
- f) proprietà meccaniche dei materiali utilizzati, tenendo conto, se del caso, di aspetti quali robustezza, duttilità, resistenza alla frattura, resistenza all’usura e resistenza alla fatica;
- g) proprietà di superficie; e
- h) la conferma che il dispositivo soddisfa tutte le specifiche chimiche e/o fisiche definite.
Come garantire sicurezza, prestazioni e affidabilità di componenti o prodotti realizzati in Additive
Nella gestione di qualunque processo di produzione, e quindi anche dei processi realizzati tramite manifattura additiva, è necessario prendere in considerazione tutti i fattori che, potenzialmente, possono alterare le proprietà e gli obiettivi prestazionali stabiliti dalle specifiche di progetto.
Possiamo quindi modellizzare concettualmente questo approccio come segue:
- Progettazione, scelta e ottimizzazione del design
- Scelta del processo di stampa, selezione dei parametri del processo e influenza di tali parametri sulle caratteristiche chimico fisiche dello stampato
- Qualifica degli operatori, in tutti i casi in cui la competenza degli stessi risulti essenziale rispetto all’esito del processo
- Scelta del materiale e validazione (proprietà meccaniche, fisiche, chimiche, metallurgiche)
- Validazione del prodotto finito (proprietà meccaniche, fisiche, chimiche, metallurgiche, correlate alle prestazioni attese e all’ambiente di utilizzo)
Scelta e ottimizzazione del design
È noto che, rispetto alla manifattura tradizionale, la Manifattura Additiva consente di realizzare componenti con forme più complesse e garantisce un’elevata libertà di design di features interne ed esterne. La possibilità di posizionare il materiale solo dove è strettamente necessario consente la riduzione del peso e l’ottimizzazione delle prestazioni, oltre alla riduzione degli sprechi di materiale. Consente infine di ridurre il numero di componenti in un assemblato. Tuttavia, un design non ottimizzato sul processo di realizzazione può alterare e compromettere le caratteristiche del prodotto, e difficilmente la replica di un design destinato a un processo manifatturiero tradizionale soddisfa i medesimi requisiti di prestazione.
Le tecniche riassunte sotto l’acronimo DfAM (Design for Additive Manufacturing, insieme di regole e best practice per la realizzazione di componenti di elevata qualità), che includono la Topology Optimization (minimizzazione del materiale e ottimizzazione delle prestazioni), le simulazioni numeriche FEM e sempre più spesso il Generative Design consentono di individuare la geometria teoricamente più idonea al tipo di processo al fine di garantire il rispetto dei requisiti di prestazione.
Il processo può tuttavia essere iterativo, perché i successivi esiti di validazione di materiale, processo e output finale possono mettere in luce potenziali difetti eliminabili solo con un diverso design. Il caso tipico è rappresentato da supporti, le strutture temporanee necessarie per sostenere le parti durante il processo di stampa, la cui rimozione al termine del processo può generare discontinuità superficiali tali da compromettere nel tempo l’integrità del prodotto finito.
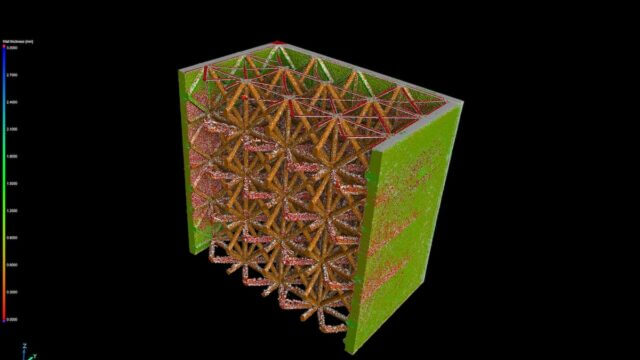
Validazione del materiale: il caso delle polveri metalliche
Come per ogni processo industriale (ma vale anche in cucina!) le caratteristiche e la qualità della materia prima sono essenziali per il risultato del processo. Nel caso delle polveri metalliche utilizzate per la realizzazione in Additive Manufacturing l’esperienza consolidata negli ultimi 25 anni suggerisce di porre particolare attenzione ai seguenti parametri:
- Distribuzione granulometrica (Particle Size Distribution – PSD)
- Composizione chimica
- Densità
- Morfologia
- Scorrevolezza
- Contaminazione
Ne consegue inoltre che per le polveri devono essere garantiti un’adeguata tracciabilità e metodi di conservazione tali da non alterarne le caratteristiche (elementi che riguardano il processo produttivo).
Il riferimento principale è costituito da due norme:
- ASTM F3049 – Standard Guide for Characterizing Properties of Metal Powders Used for Additive Manufactiring Processes
- ISO/ASTM 52907 – Additive Manufacturing, Feedstock Materials, Methods to characterize metal powders
La distribuzione granulometrica delle polveri (PSD) si riferisce alla distribuzione delle dimensioni delle particelle in un campione di polvere. La dimensione delle particelle di polvere influenza lo spessore minimo realizzabile, la dimensione minima del dettaglio realizzabile e la rugosità e la finitura superficiale del componente stampato. Una distribuzione non uniforme può generare problemi in corso di stampa o sulla qualità del prodotto finito. Vi sono quindi tecniche analitiche specifiche (setacci, analisi di immagini mediante microscopia elettronica a scansione (SEM) e Microscopio ottico, Light scattering, Laser diffraction method) che consentono di valutare questa caratteristica.
La composizione chimica della polvere deve essere omogenea, controllata e nota per poter garantire buone proprietà del manufatto finale. La presenza di inclusioni potrebbe influenzare e alterare la cinetica del bagno fuso, causare tensioni residue e generare difetti interni. La composizione chimica influenza, infatti, la temperatura di fusione, le proprietà meccaniche, la saldabilità e le proprietà termiche.
Un’altra caratteristica che influenza inesorabilmente il processo di stampa è la scorrevolezza, definita come la capacità della polvere di fluire lungo una pendenza o attraverso un foro sotto effetto della sola forza di gravità. In particolare, particelle fini e di forma irregolare sono caratterizzate da bassa scorrevolezza. Particelle sferiche sono preferibili grazie ad una più elevata scorrevolezza.
Infine, la forma delle particelle di polvere (morfologia) influenza fortemente la loro capacità di impacchettarsi e di fluire, e ha quindi impatto sul processo produttivo. Anche in questo caso l’analisi SEM o CT Scan fornisce elementi utili alla valutazione.
Validazione del processo di Manifattura Additiva
La validazione del processo riguarda l’insieme di valutazioni orientate a garantire l’esito mediante analisi che – per costo e natura – non potranno essere effettuate successivamente su tutti i prodotti realizzati. Si tratta per la maggior parte di verifiche di carattere distruttivo effettuate su provini di materiale, per le quali i livelli di accettabilità dipendono non solo da normative di prodotto ma anche dalle specifiche di progetto e dalle necessità definite dall’utilizzo finale.
In particolare, ci riferiamo a valutazioni concernenti i seguenti aspetti:
- Conformità metallurgica
- Difettosità interne e porosità
- Proprietà meccaniche
- Geometria e dimensioni
- Proprietà chimiche
- Rugosità e finitura superficiale
La condizione metallurgica è strettamente legata alle caratteristiche meccaniche e quindi al comportamento in esercizio. La microstruttura deve presentare una morfologia adeguata e compatibile con l’utilizzo, regolata da norme di prodotto.
I principali fattori che influenzano la microstruttura sono il tipo di processo, i parametri di stampa, i trattamenti termici a cui è sottoposto il prodotto stampato.
La conformità è valutata secondo criteri consolidati nell’analisi metallurgica. In particolare:
- I campioni devono essere prelevati da zone significative del componente o stampati appositamente nelle vicinanze del componente finale.
- I campioni devono essere analizzati secondo la direzione XY e lungo la direzione di stampa Z.
- Le superfici devono essere preparate metallograficamente secondo le già note normative della metallurgia, quali ASTM E3, ASTM E407.
- La microstruttura deve risultare coerente con le aspettative (tenendo in considerazione processo di stampa e trattamenti termici), priva di cricche e di difetti di origine metallurgica.
- La dimensione del grano deve essere valutata lungo la direzione trasversale e longitudinale del campione.
- Le inclusioni non metalliche devono essere valutate e, possibilmente, classificate.
Difettosità interne e porosità possono essere valutate tramite analisi al microscopio ottico e analisi SEM, oppure analisi non distruttive del componente finale, di un prototipo o di un provino stampato appositamente tramite scansione tomografica CT.
Infine, le proprietà meccaniche prevedono l’identificazione di prove definite in funzione del tipo di componente, dell’applicazione e della criticità. Si possono prevedere prove di durezza, test di trazione e/o di compressione, test di resilienza e piega, prove di fatica. Per l’esecuzione di queste prove è determinante la selezione dei provini, che devono essere ricavati tenendo in considerazione l’influenza della direzione di stampa sulle proprietà finali del componente. I test devono essere svolti sul materiale al termine del suo ciclo di trattamenti termici, e possono essere svolti a temperatura ambiente o ad una temperatura diversa in accordo alle specifiche di progetto e a seconda dell’impiego finale dell’oggetto.
Validazione del prodotto: le prove di tipo
Rispetto ai test eseguiti sui provini preliminari standardizzati, il componente finale ha proprietà che possono differire da quelle studiate in fase di qualifica di processo.
I fattori che influenzano le caratteristiche dei prodotti finali sono, tra le altre:
- La geometria del componente
- L’orientamento della parte nel letto di stampa
- Il posizionamento dei supporti
- La vicinanza tra componenti stampati contemporaneamente
- La presenza di componenti impilati
- L’utilizzo di laser multipli
Si definiscono “prove di tipo” le prove effettuate su uno o più campioni rappresentativi di una più ampia produzione. Sono effettuate ogni volta vengano modificate le caratteristiche del prodotto o del processo, e sono tipicamente richieste dalle principali leggi e direttive che regolano l’immissione in commercio dei prodotti.
Le prove di tipo riguardano la caratterizzazione del prodotto finito. Vengono valutate le proprietà meccaniche (Resistenza a trazione, carico, fatica, etc.), le tensioni residue, la struttura metallografica. La resistenza alla corrosione diventa fondamentale per i prodotti sottoposti a condizioni di utilizzo particolari (umidità, atmosfere saline, contatto con fluidi corrosivi etc.). Altrettanta attenzione deve essere posta a difettosità interna , porosità, rugosità e finitura superficiale
Le prove distruttive e non distruttive
Le prove possono poi essere classificate in funzione dell’impatto sul campione analizzato, in prove distruttive e non distruttive.
Tra le prove distruttive è opportuno sottolineare le prove tese a verificare nel tempo il comportamento del prodotto soggetto alle sollecitazioni prevedibili nel corso della sua vita utile. Le prove di fatica vengono generalmente svolte sul componente finito, post trattamenti termici e in seguito ai processi di finitura superficiale. Tuttavia, i test ciclici a fatica possono essere svolti anche su prototipi o su provini che simulano le condizioni di sollecitazione più sfavorevoli per il componente finale stesso. La norma ISO/ASTM 52908 – Additive Manufacturing, Finished part properties, Post-processing, inspection and testing of parts produced by powder bed fusion può rappresentare un riferimento utile per la definizione di questo tipo di prove.
Le prove non distruttive comprendono in particolare le verifiche dimensionali e il controllo difettologico effettuato con Tomografia Industriale (CT-scan).
Queste ultime, che per loro natura non compromettono l’integrità del prodotto, possono essere ripetute periodicamente per garantire il permanere delle caratteristiche. L’analisi tomografica consente di effettuare confronti CAD nominale/reale, controlli geometrici e dimensionali, verifica della presenza di difetti interni legati al processo di stampa ed esami quantitativi della porosità interna del componente che può influenzarne le caratteristiche di resistenza.
La certificazione del prodotto realizzato in Manifattura Additiva
La certificazione del prodotto può essere obbligatoria (cogente) se la tipologia del prodotto è soggetta a specifiche legislazioni (es. se si tratta di un dispositivo medico, o di un prodotto in pressione) oppure volontaria se effettuata per scelta del produttore (o per richiesta del committente).
In ogni caso quando parliamo di certificazione di prodotto intendiamo un processo di valutazione che riguarda da un lato le caratteristiche del prodotto stesso, dall’altro le caratteristiche del processo produttivo. I principali schemi di certificazione sono quindi basati su rapporti di prova relativi a campioni rappresentativi della produzione e da attività di carattere ispettivo sul processo di fabbrica; questi ultimi sono orientati a valutare in quale misura la variabilità della produzione sia mantenuta entro limiti tollerabili grazie a procedure di produzione validate, un corretto processo di approvvigionamento delle materie prime, strumenti di controllo tarati, competenze del personale, processi di controllo e collaudo finale etc.
Anche per la manifattura additiva è quindi necessario che il processo produttivo applichi le ormai consolidate tecniche di gestione della qualità, e che si provveda a periodici audit interni sul rispetto di tali requisiti.
Progettare la conformità normativa
Come abbiamo visto rapidamente, per garantire la conformità di un componente e di un prodotto e renderne possibile la commercializzazione è necessario effettuare numerose attività di indagine e tenere sotto controllo una mole importante di fattori che possono influenzare l’esito dei processi.
La conformità normativa è quindi un tema che merita e necessita di essere progettato in parallelo allo sviluppo di un nuovo prodotto, perché risulta determinante ai fini dell’accesso al mercato e richiede fasi, tempi e costi che devono essere definiti in anticipo per evitare ritardi nel time-to-market e/o costi extra budget. La collaborazione tra produttore, organismo di certificazione e laboratorio consente di acquisire consapevolezza delle esigenze, individuare le normative applicabili, definire il programma delle prove, individuare i processi critici per i quali sarà necessario definire procedure validate. L’obiettivo finale è quello di favorire la competitività dell’impresa consentendo un accesso sicuro ai mercati di riferimento.
L'articolo Manifattura Additiva, perché è importante validare i processi produttivi e certificare il prodotto proviene da Innovation Post.
Qual è la vostra reazione?






